Less effort in reusable packaging management: meta reorganises load carrier management
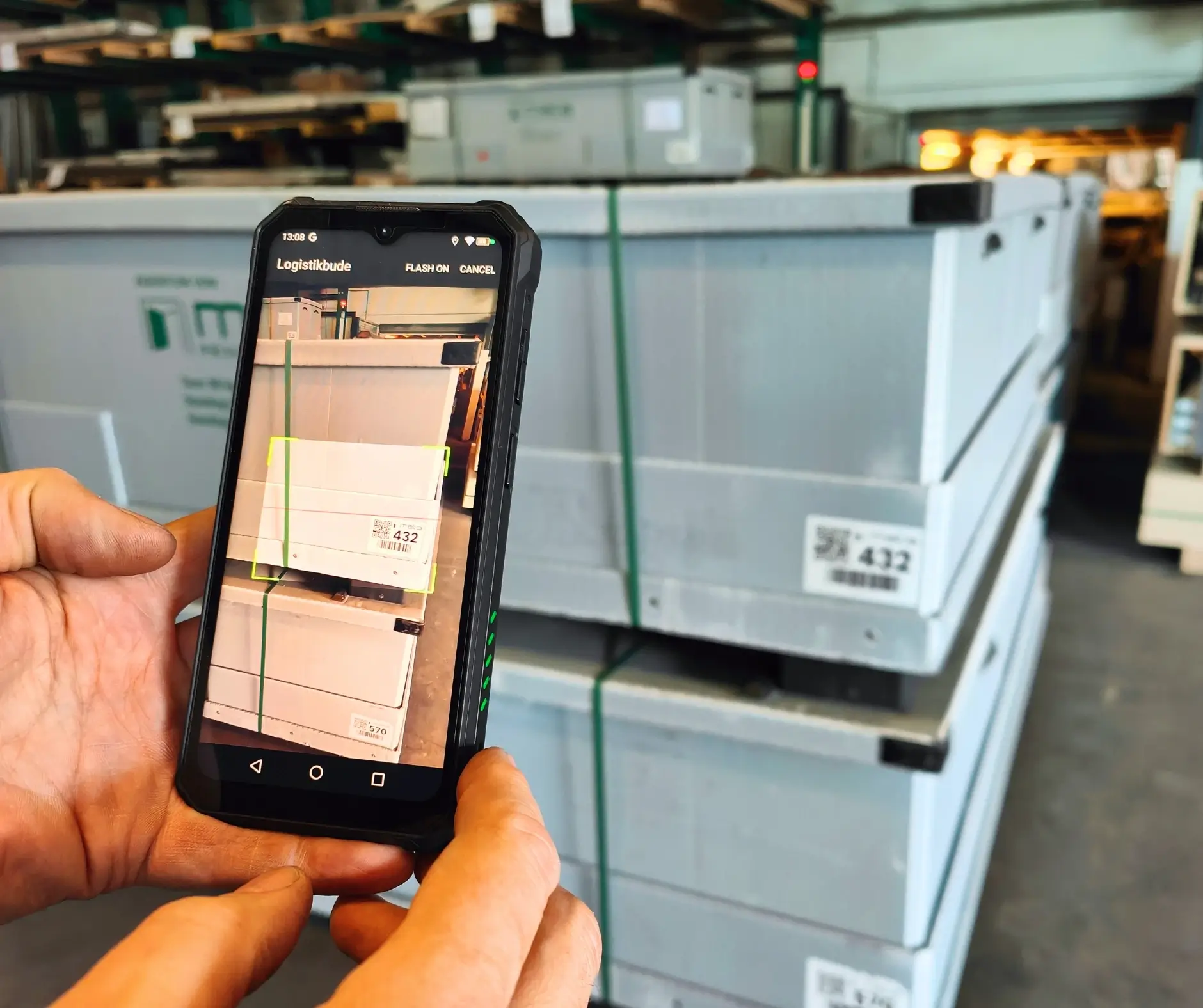
The leading manufacturer of toilet partition systems not only reduces disposable containers in its supply chain - thanks to the Logistikbude, it also keeps track of its load carriers at all times and can plan them more efficiently.
Packaging waste is never good. Especially not when it can be avoided. In order to position itself more sustainably, meta Trennwandanlagen GmbH & Co. KG from Rengsdorf has set itself the goal of relying almost entirely on reusable packaging. ‘In the course of switching to reusable packaging, we realised that we needed software that would allow us to track our containers,’ says Matthias Ehrenstein, Head of IT at meta Trennwandanlagen, describing the initial situation.
Counteract high shrinkage costs and high personnel costs
Otherwise, the Rengsdorf-based company would lose sight of them in the value chain, which would result in high shrinkage costs. Alternatively, the employees would have to manually track the containers in painstaking detail - also cost-intensive due to the many hours of work involved.
meta normally develops such software solutions itself. Thanks to its modern production technology and software, the Rengsdorf-based company has become one of the leading manufacturers of toilet partition systems in Europe. In this case, however, the development time and costs were uneconomical - partly because the right software solution was found straight away.
Making reusable objects digitally discoverable
‘Our software makes it possible to manage all reusable objects in one solution. meta's challenge is not an isolated case; many manufacturing companies have problems with load carrier management,’ explains Steffen Brand, Customer Success Manager at Logistikbude. This is why the Dortmund-based start-up has dedicated itself to the digitalisation of reusable management. The ‘Bude’ defines reusable objects as pallets, boxes, containers, racks - in other words, everything that is used between or within companies. Logistikbude is a cloud-based software that tracks all these containers in real time and displays them online.
After switching to reusable containers, meta now has over 600 reusable crates in four different designs. They are equipped with a unique identification number, i.e. serialised, and can be scanned at the various company and partner locations thanks to the Logistikbude companion application.
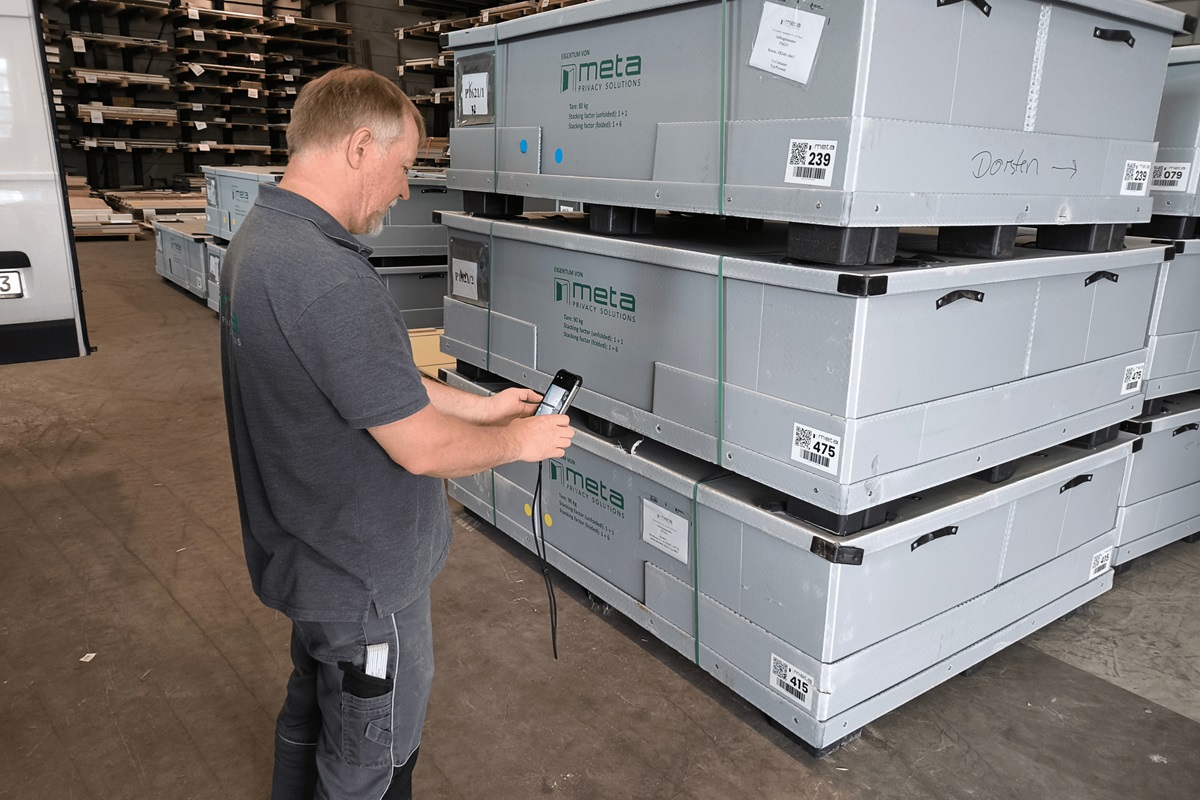
Monitor and manage containers in real time
After the scanning process, the app not only makes the inventory of containers at all locations directly visible, but also their history: ‘For each crate, for example, the number of location changes, their transport route or their age can be traced directly. The condition of the crates is also recorded. meta can clearly track when and where they have been damaged at any time,’ explains Brand. Logistikbude also displays this clearly in a dashboard so that the partition wall manufacturer can take action at an early stage if there are a large number of defective crates at one location.
Ehrenstein: ‘Thanks to Logistikbude, we have load carrier management in real time. This helps us to keep an eye on the utilisation of our containers and plan ahead.’
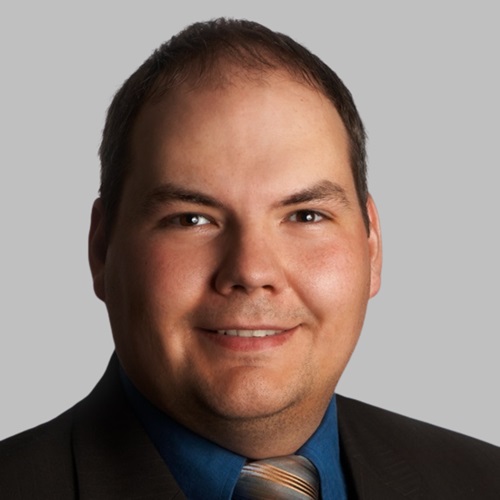
Quick integration into everyday working life
The integration into meta's day-to-day work was completed in a short space of time. During a short test phase, the Dortmund-based start-up added customised configurations for the partition specialist and incorporated individual wishes in terms of usability. Overall, the customisations were minimal. ‘Our standard software was already tailored to the area of application at meta, so there was no need for a lengthy implementation project,’ explains Brand. It took less than two months from the first contact to the final integration into everyday working life.
Brand: ‘One of our goals is to go live with the software as soon as possible. It should be ready for use quickly and intuitive to operate so that the improvements in the workflow can be realised immediately.’
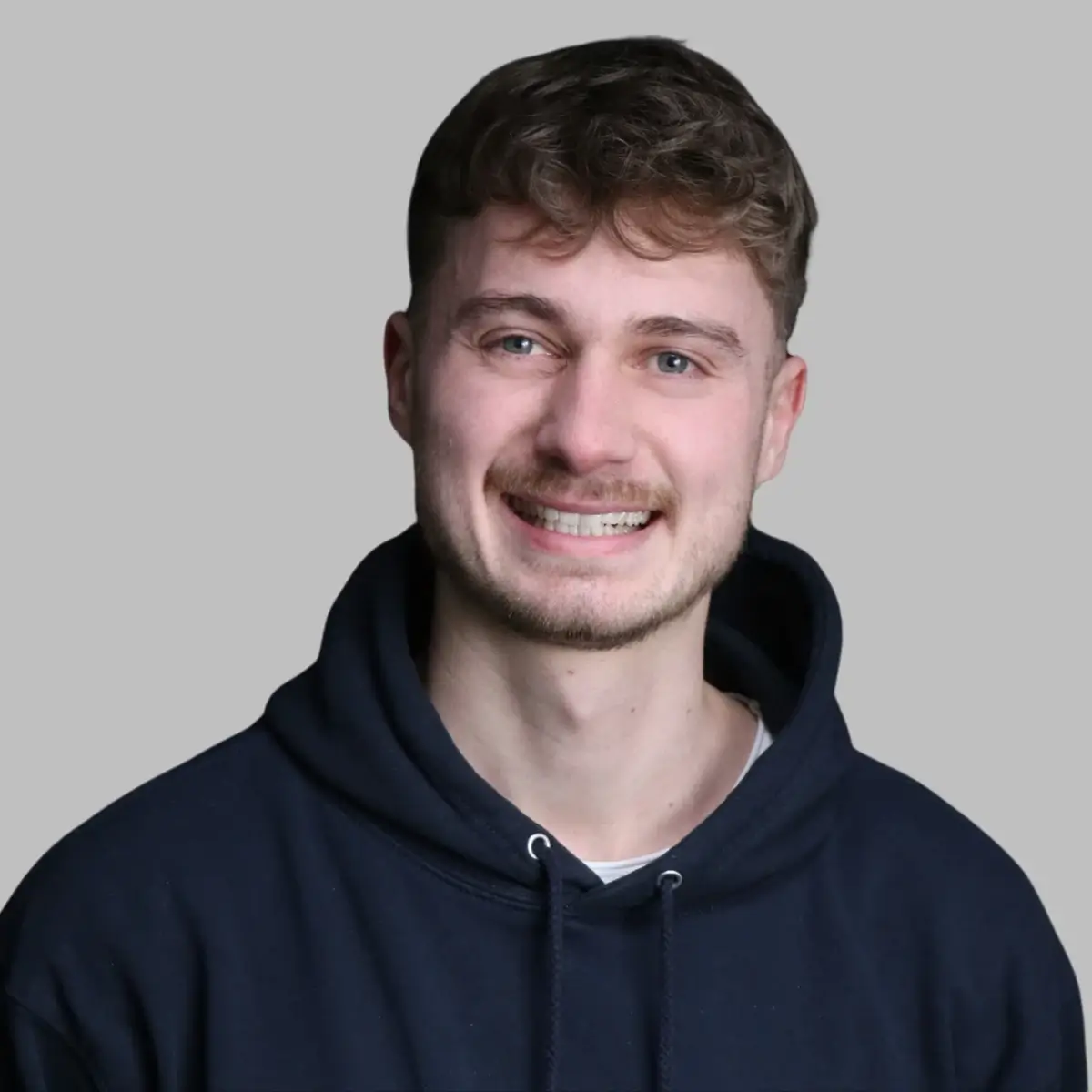
Ideally positioned for EU packaging regulations
The reorganisation of its packaging management in combination with its administration via software makes meta doubly future-proof: On the one hand, reusable containers reduce packaging waste and are therefore more environmentally friendly than disposable alternatives. At the same time, the company is prepared for legislation that will become important in the future, such as the planned EU Packaging & Packaging Waste Regulation (PPWR). In addition to a reusable packaging obligation in B2B transport, this will also include a labelling obligation for the containers used - both points that meta has already implemented and is ahead of its competitors.
About Logistikbude
Logistikbude, a logistics start-up founded in 2021, digitalises the management of reusable assets such as pallets, containers and racks. Its user-friendly software creates transparency about stocks, requirements and turnaround times. Shippers, logistics service providers and retailers benefit from lower repurchase rates and reduced administrative costs.
The experts at Logistikbude are also happy to share their many years of experience from the world of packaging at Fraunhofer IML in a non-binding exchange, over a digital coffee or at events. Get in touch at any time using the contact form.
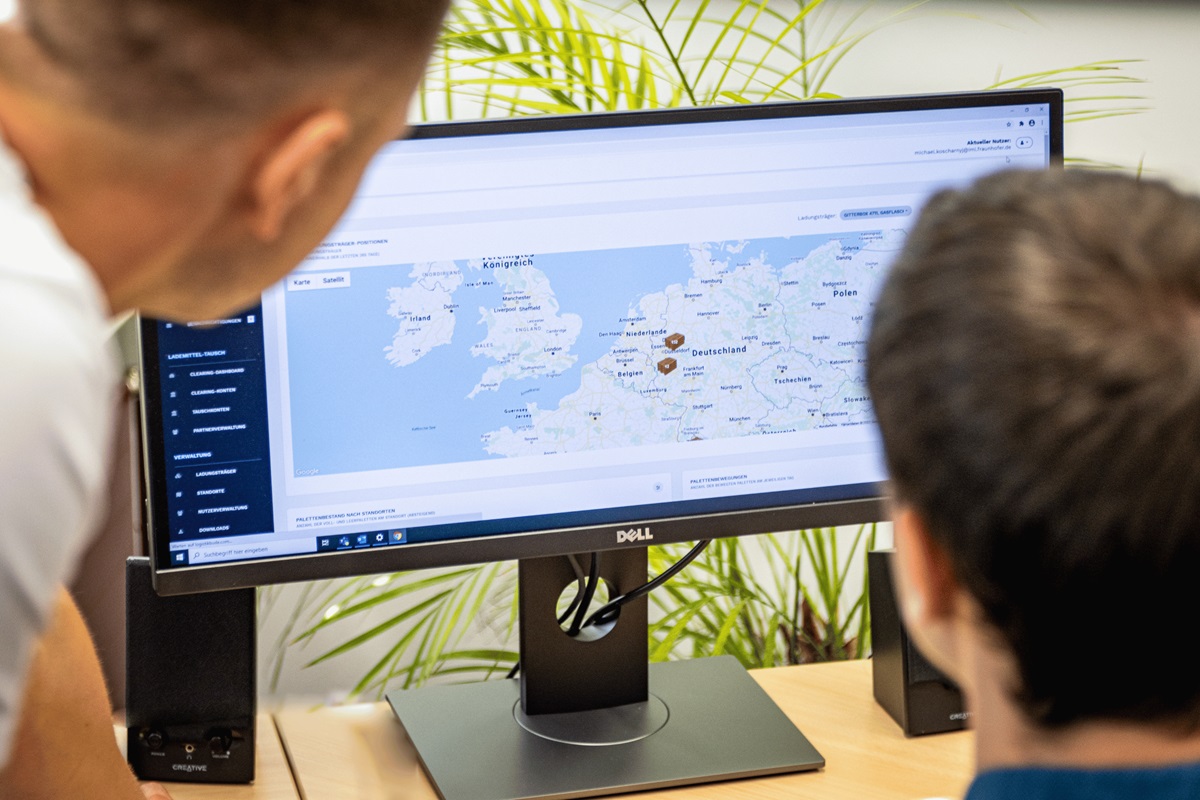
Schedule a free consultation now!
We would like to get to know you and your current challenges with reusable objects. As a first step, we analyse your status quo together and check where there is potential for optimization and automation. If we have a suitable solution for you, we will present our solution to you on your use case in a second appointment.