Always keeping an eye on empties: HAWE Hydraulik SE raises container management to a new level of transparency
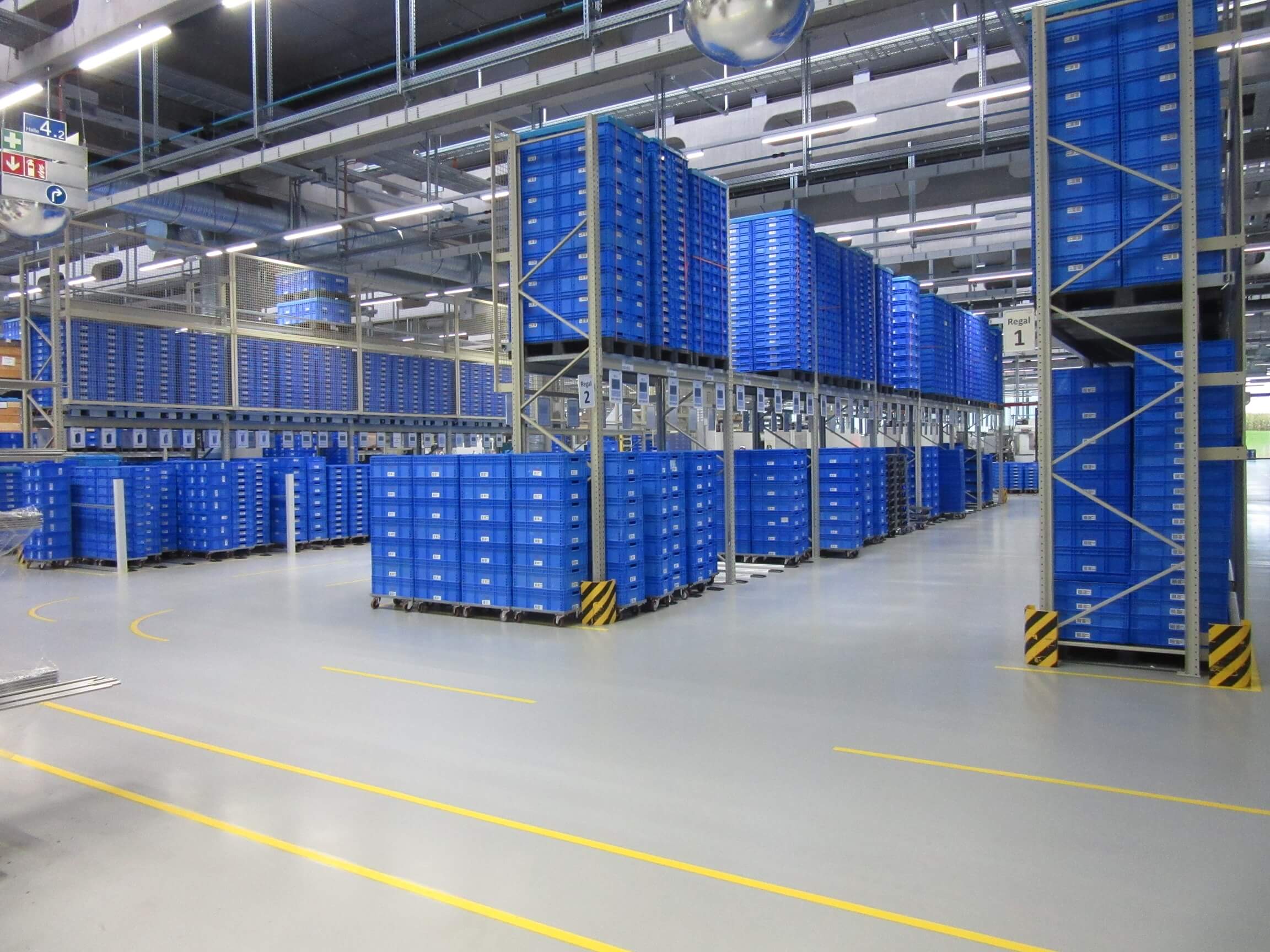
The manufacturer of hydraulic parts bundles all information about its empty containers in the Logistikbude's software solution. Thanks to streamlined coordination processes, HAWE not only simplifies communication with suppliers, but also avoids unnecessary new purchases by providing a better overview of the containers.
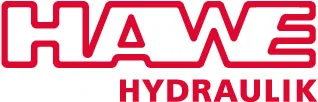
HAWE Hydraulik SE is a family company headquartered in Munich, which manufactures various hydraulic components in its own production plants and delivers them internationally to its customers. With over 70 years of experience in the hydraulics sector and the integration of technical innovations, HAWE offers tailor-made solutions for a wide range of industries and areas of application — from mechanical engineering to agriculture and the renewable energy sector.
Simple empties management without tracking options
As a manufacturer of diverse hydraulic systems, the family-owned company has large quantities of reusable load carriers in circulation to transport the products, whether within its own plants, from plant to plant or for delivery to customers. Christian Jasch is responsible for this. As a container management employee, he ensures that suppliers always have enough empty containers available to supply HAWE with semi-finished products and raw materials for production. Until now, this process has been kept very streamlined: Suppliers placed container orders from Jasch via email. He processed the orders and confirmed them before the empties were finally shipped. However, important information was missing afterwards, as it was never clear exactly where the respective containers and pallets were actually located. This was partly due to the fact that HAWE received hardly any feedback as to whether the empty containers had even reached the supplier — this step was missing from the process so far. In addition, communication via email offered potential for errors as soon as information was not forwarded to the responsible persons.
“We had to communicate on various channels, painstakingly collect information, coordinate everything and constantly coordinate,” explains Jasch.
As a result of these problems and the lack of traceability, HAWE wanted to fundamentally revise the container management process and optimize internal processing. Klaus Stadtmüller, responsible for shipping at HAWE, was also already aware of the problem. This is because the containers have a high purchase value, meaning that losing them is expensive. Together with his colleagues, he decided to look for a suitable solution.
“We always wanted to know exactly how many containers are currently with which supplier, how long they have been on the road and when, or whether they were returned at all,” explains Stadtmüller. “For this, we needed a modern, uncomplicated and, above all, uniform system that brings together all information about our empties and bundles all container management processes in one tool. ”
He found what he was looking for on the same day as he became aware of the Logistikbude in a newspaper article.
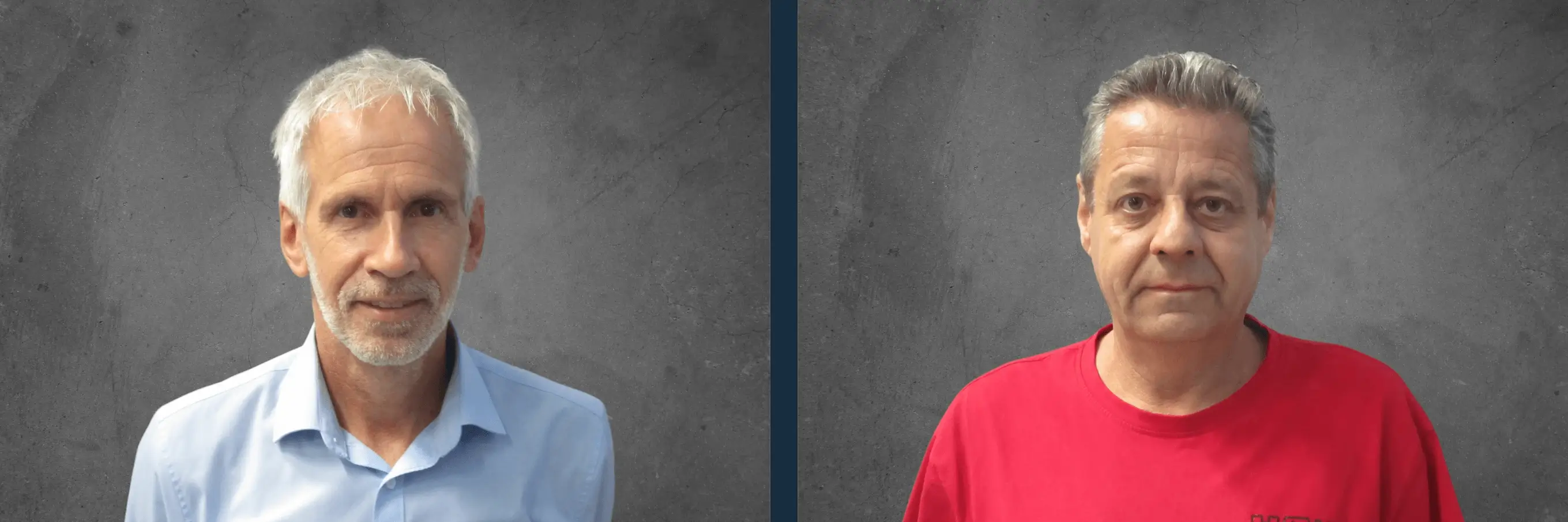
Confirmation in just three clicks
The cloud-based software solution Logistikbude has expanded the management of containers at HAWE and at the same time standardized internal processing processes. Suppliers are now being more closely involved in this process to ensure a continuous and reliable supply of information. The majority of empty goods orders are now placed using the Logistikbude's software, so that Jasch can process them directly. As soon as the containers have arrived at the supplier, they confirm their acceptance via a link — and in just three clicks, without logging in or having an account, as is the case with comparable applications. Instead of having to log in laboriously or manually enter container quantities into portals, the suppliers only see the information relevant to them via the link, directly at a glance. For HAWE, this was the decisive criterion when choosing the logistics shed: “It was particularly important to us that our suppliers have as little work as possible when they use the logistics shed system together with us. The solution should be quick, intuitive and easy to use for everyone involved,” explains Stadtmüller.
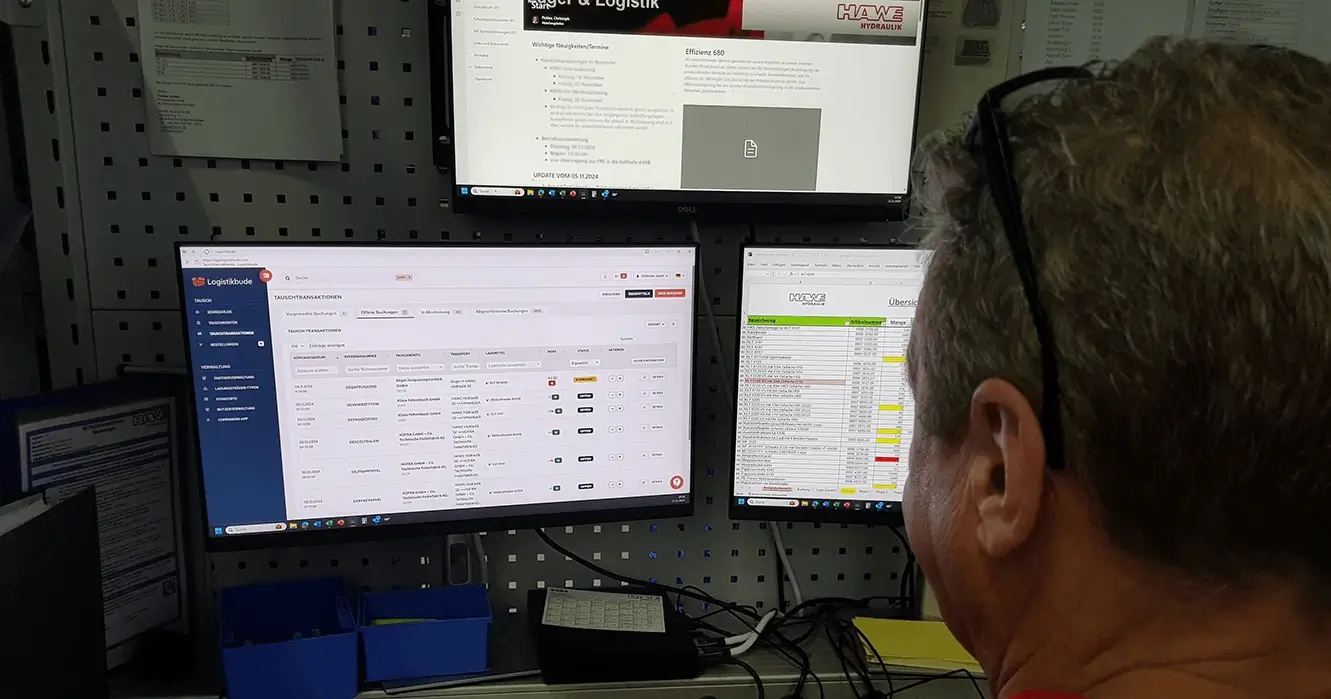
If the containers are returned to HAWE, receipt is also confirmed there. Because HAWE uses the same account in the Logistikbude for all locations, it is easy to use across the company. The inventory of reusable objects, such as small load carriers (KLTs), covers or even special pallets, is coordinated at all times between the participating suppliers and HAWE employees: “There is no need for manual clarification about the status of empty containers. This makes everyday life and, above all, communication with one another much easier,” says Jasch. Another major advantage of the solution: Suppliers can continue to order directly from Jasch by email or telephone, who simply logs the information into the system retrospectively. In this way, all steps of the process are still controlled centrally via the logistics shed software, which brings together all communication channels — regardless of which ordering method is preferred.
Save costs through more efficient planning
In addition, Jasch and his team can track the containers that are in circulation in real time on the Logistikbude portal. This transparency benefits various departments, in particular Purchasing, which is responsible for procuring the new containers. With the help of the data collected with the Logistikbude, budget planning is easier because the required quantities are always visible and comprehensible.
“The benefits of the new process are enormous — in particular due to the savings we achieve because no more containers are lost or purchased superfluously,” explains Stadtmüller.
Comprehensive support services for employees and suppliers
After the initial contact, it quickly became clear that the Logistikbude's solution was an ideal fit for HAWE's requirements. As one of the first customers of the Logistikbude ever, the manufacturer of hydraulic components was intensively supported by co-founder and COO Michael Koscharnyj in the implementation of the logistics shed.
“The success of this project was also particularly important for us, as it was the first time that we had implemented a comprehensive container management system in this form,” explains Koscharnyj. “In doing so, we have paved the way for future use cases and gained valuable experience, which has significantly advanced our development and improvement of the product. In particular, the excellent collaboration with the HAWE team has contributed to this mutual success. ”
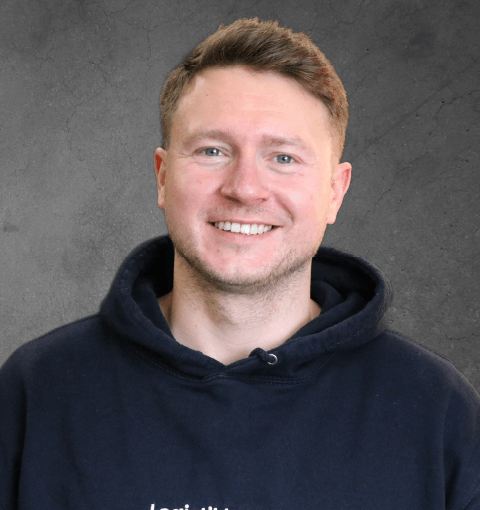
During implementation, the hydraulic manufacturer took time to optimally prepare all employees and suppliers involved for the changeover. In order to understand immediately in advance where there might be difficulties in implementation, a number of “pilot suppliers” were selected, who tested the solution and provided valuable feedback, in particular on the support offers. Because in order to make handling as easy as possible, the Logistikbude designed informative handouts and instructions. In addition, the HAWE team was intensively trained in how to use the tool. The final implementation was then carried out quickly: “Whenever we wanted to go one step further during the pilot phase, the Logistikbude team was there to help us,” says Stadtmüller. “With this support, we were able to overcome the challenges of both introductions quickly and easily.” Even after the successful implementation of the new system, the Logistikbude is supporting the hydraulic manufacturer and is continuously developing its solution.
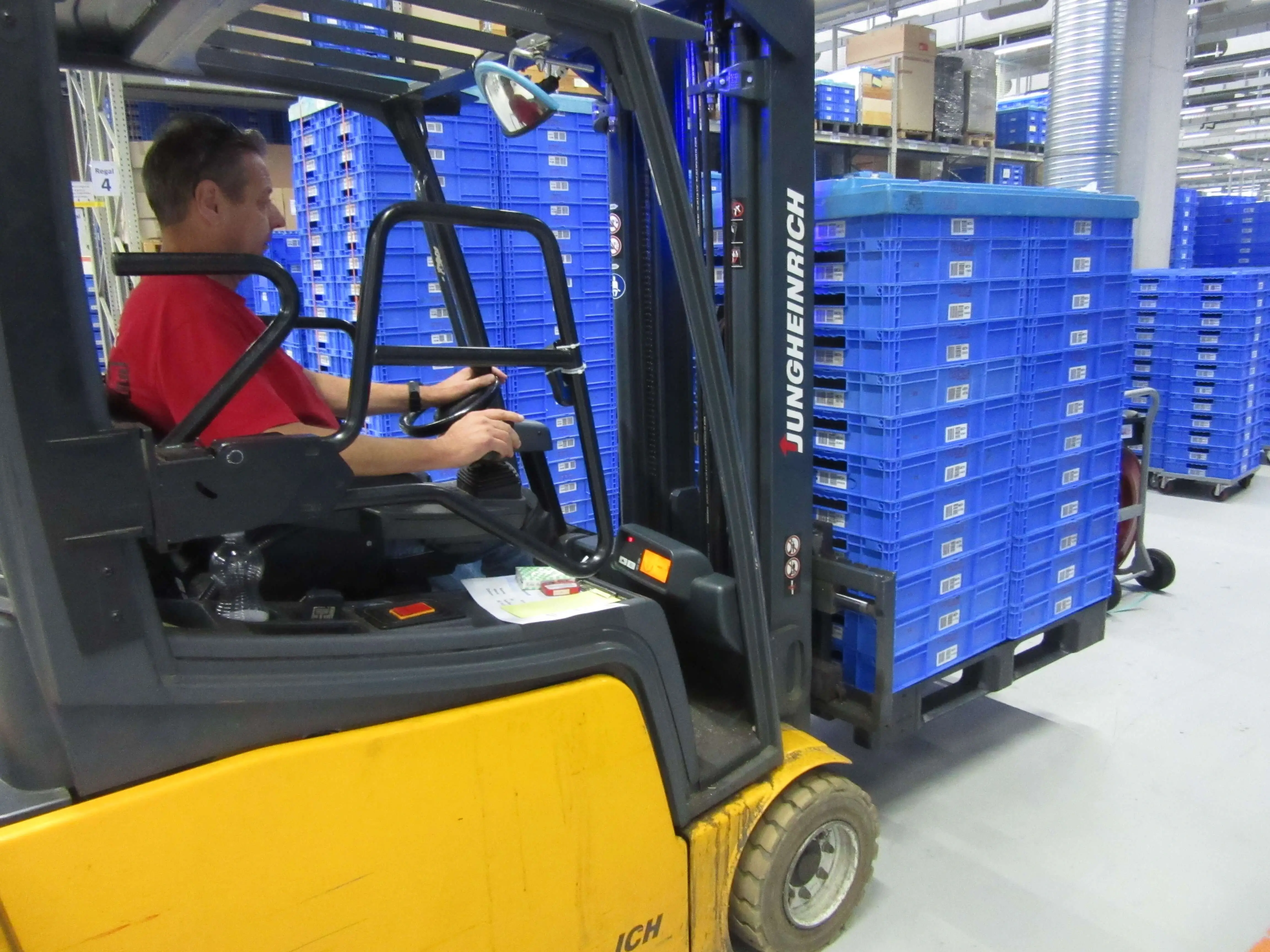
Complete satisfaction through goal-oriented cooperation
It is also possible to use the system in other areas: “We also have numerous containers on the move internally. We could therefore imagine scaling the Logistikbude to individual departments in the future,” says Stadtmüller. He and his team have already considered the previous project a success: “The cooperation with the Logistikbude was consistently pleasant, smooth and very satisfactory — a partnership that we can definitely recommend. ”
Schedule a free consultation now!
We would like to get to know you and your current challenges with reusable objects. As a first step, we analyse your status quo together and check where there is potential for optimization and automation. If we have a suitable solution for you, we will present our solution to you on your use case in a second appointment.