Efficiency meets sustainability: How PaLog's digital pallet management strengthens the circular economy
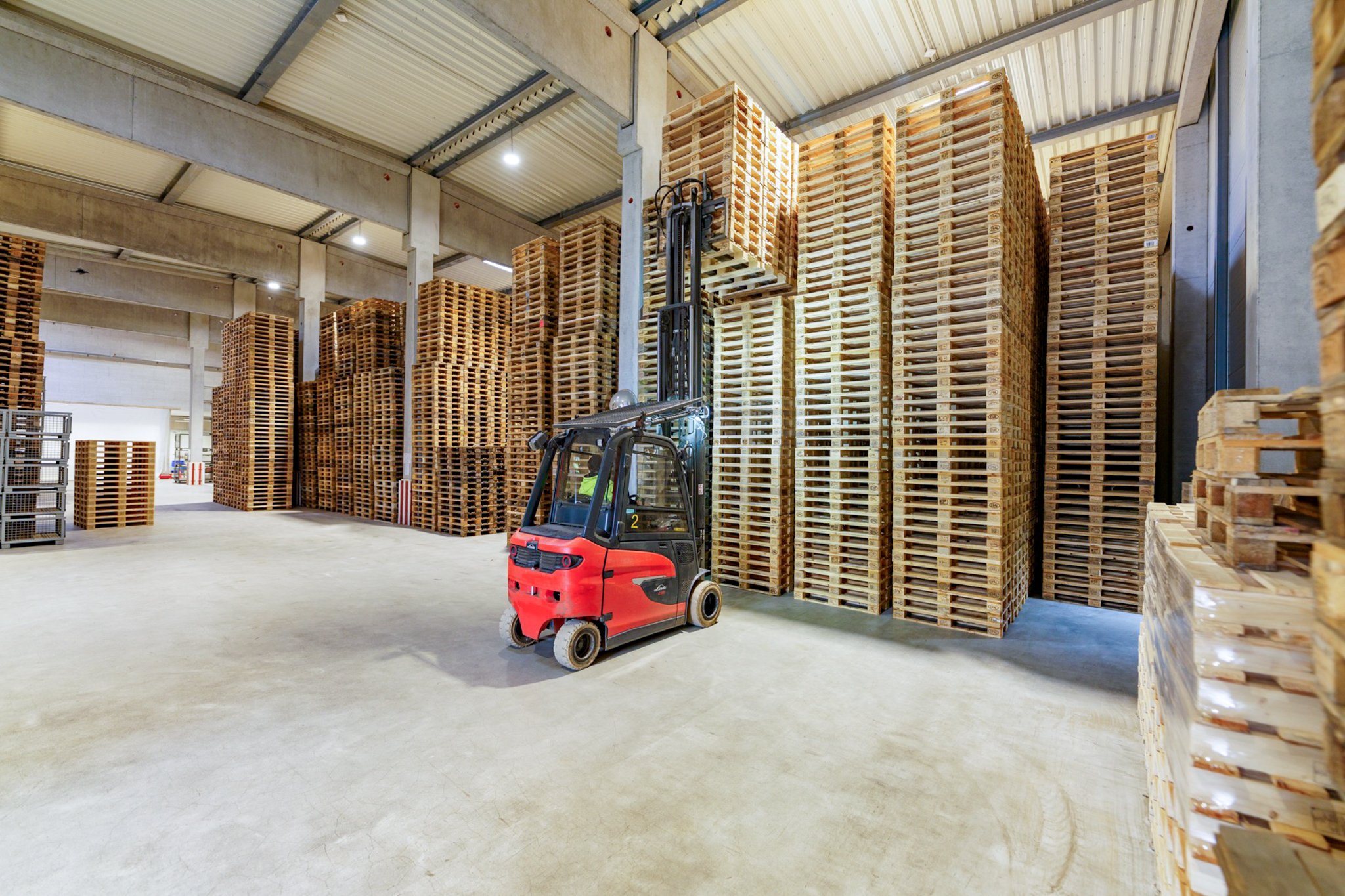
Thanks to the cloud-based software solution from Logistikbude, PaLog Palettenlogistik-Systeme GmbH can track where its pallets are at all times - and significantly reduce the workload on its employees thanks to the optimised booking processes. The increased efficiency has enabled the pooling provider to increase its turnover by around 20 per cent without hiring additional staff in load carrier management. The digital solution also contributes to a more sustainable circular economy.
The PALETTEN-SERVICE Hamburg Group specialises in load carriers: with five of its own production sites, around 240 employees and an international partner network, the Group supplies its customers throughout Europe with more than 10 million pallets and pallet cages per year. The group includes eight medium-sized companies based in Germany and Poland, which handle various logistics processes - from storage and transport to load carrier pooling. The latter is handled by the subsidiary PaLog.

Sustainable circular economy
PaLog manages its customers' entire load carrier cycle. The pooling provider buys newly produced pallets from the PALETTEN-SERVICE Hamburg Group and then delivers them to the customer. The customer uses them to handle their transport and then returns the used pallets to one of the 40 PaLog depots. Once there, they are carefully checked, repaired if damaged and sorted according to quality categories A, B and C. In this way, pallets can be made available to the next customer as required. Sustainability and the environmentally friendly use of resources play a particularly important role for the pooling provider: instead of buying new pallets for each transport, the service life of a reusable load carrier is extended. This reduces the consumption of raw materials and energy and strengthens the circular economy.
To keep track of all rental and exchange processes, PaLog records them in each customer's account. These booking processes are managed by Carola Pries, who has been a clerk at PaLog since 2010 and is the project manager responsible for implementing the logistics centre.
Ban handwritten receipt slips from work processes
For a long time, she recorded receipts by hand, posted them manually to the relevant customers and sent out accounting files at the end of the month.
Pries explains: ‘Information about stock levels was entered on traditional receipt slips and then sent by post or email. There were around 1,000 receipts per month. The administrative processes were therefore time-consuming. It took around 57 working hours per month just to enter and send stock information.’
Although PaLog maintained a simple digital database early on in which the pallet accounts could be called up, the team had to enter all the information on the load carriers manually. As only PaLog employees had access to the database, they also had to regularly check stock enquiries from customers in the software and provide information on the whereabouts of the pallets by telephone.
In order to further digitalise all of these processes, but also to make them more transparent, efficient, resource-saving and less error-prone, PaLog wanted to develop further - and found a partner in Logistikbude. The founders of the future start-up were already working at the Fraunhofer IML when they came into contact through a joint IT project. Together, they wanted to develop the right solution to meet the special requirements of the pooling provider.
Cloud-based, resource-saving booking processes
The aim of the collaboration was to digitalise load carrier management to such an extent that all partners, customers and freight forwarders involved in the exchange have an insight into current stocks at all times. Thanks to Logistikbude's cloud-based technology, this is no longer a problem: the software offers everyone involved in the exchange process transparent, real-time tracking of the pallets and provides a comprehensive overview of stocks, requirements and turnaround times. In addition, employees at PaLog depots and freight forwarders can enter booking processes and make stock changes directly in the application. This saves PaLog the diversions from the manually completed receipt slip to the system and not only avoids unnecessary work steps, but also transmission errors that can arise from these media disruptions. The effects of these streamlined work processes are clearly noticeable.
Daniel Stadach, COO of the PALETTEN-SERVICE Hamburg Group, summarises: ‘Thanks to Logistikbude, we have been able to position ourselves much better as a company: We have increased our turnover by around 20 per cent since the software was introduced without hiring additional staff.’
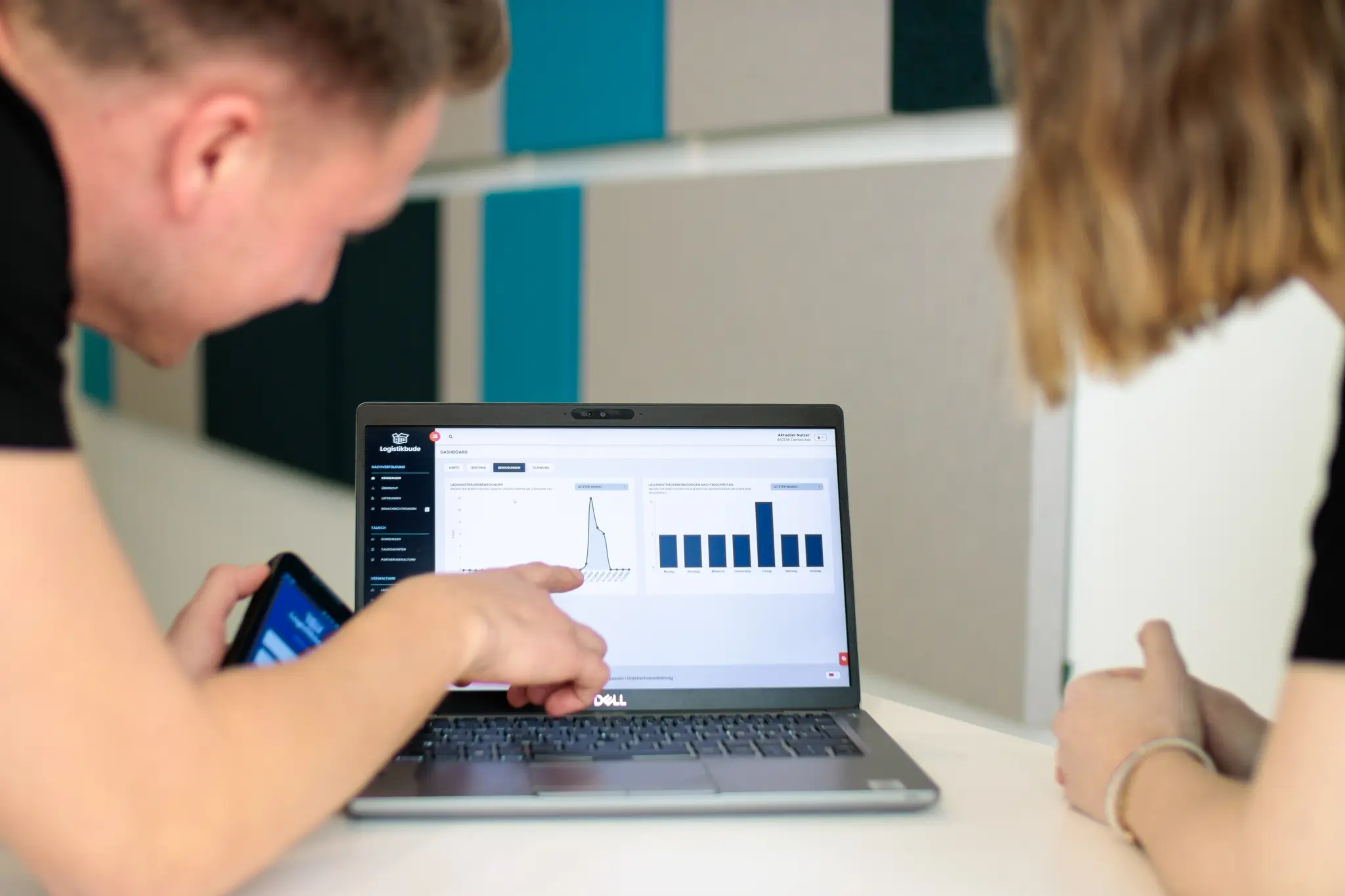
Further extending the service life of load carriers
The increased efficiency also has a positive effect on the responsible use of resources: The pallets remain in circulation for longer thanks to the transparent exchange overview of the logistics centre and thus contribute to an even more economical circular economy.
‘For us as a pooling provider, the circular economy is the central component of our corporate philosophy: renting and exchanging pallets instead of buying new ones. Being able to make this process even more sustainable by extending the service life of the load carriers is a matter close to our hearts.’
Another positive side effect of digitising its load carrier management: PaLog saves on receipts, paper and postage and takes a decisive step towards paperless administration.
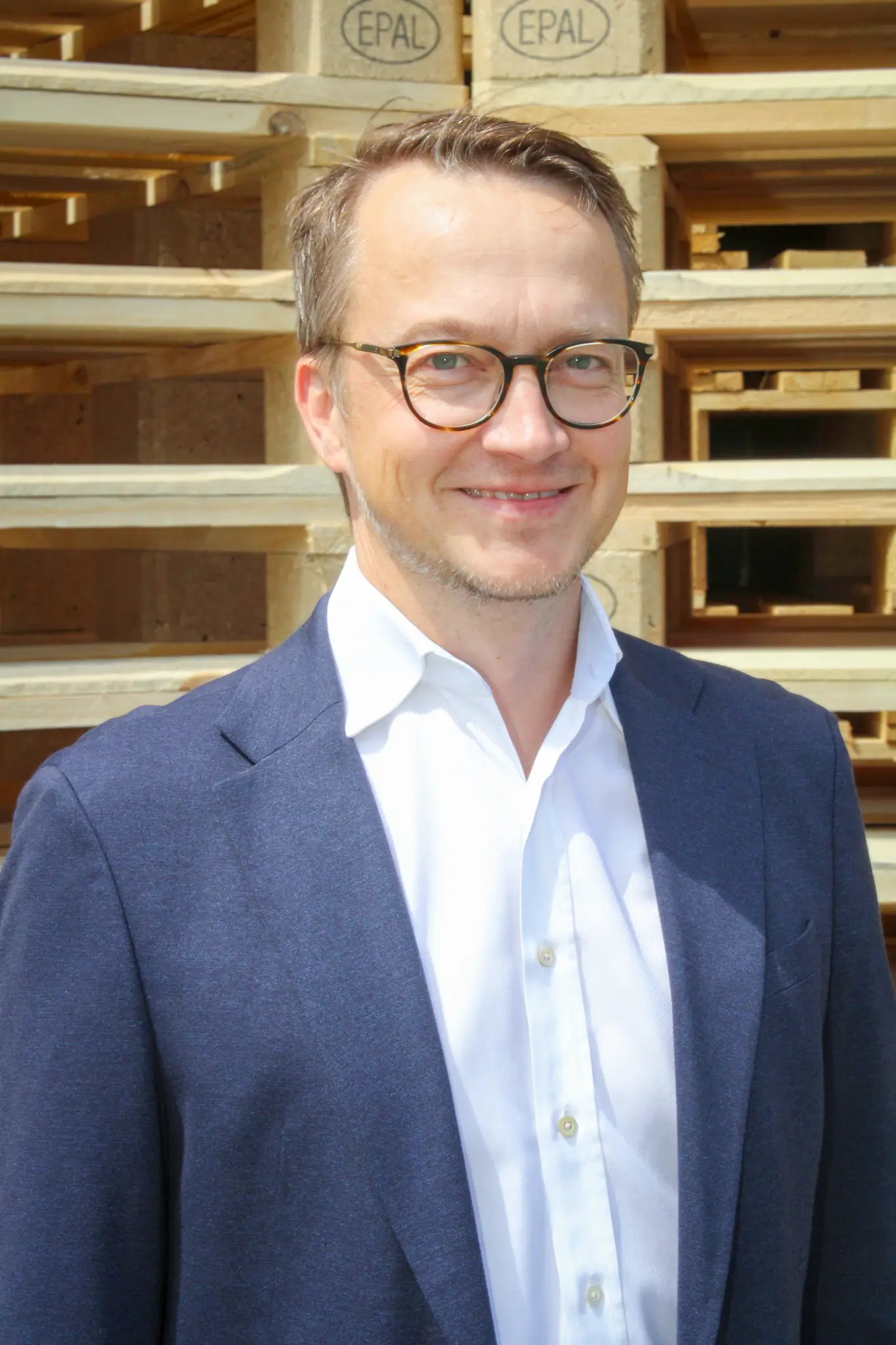
Targeted training
For the targeted implementation, the Logistikbude solution was first tested and evaluated in a test depot before being customised and finally rolled out to all 40 locations. The first step was to digitally record deliveries directly at the depot in order to simplify the booking processes. ‘After the test phase, we customised the software to our needs together with the Logistikbude team,’ says Stadach. It was particularly important that the depot employees were able to familiarise themselves intensively with the software on site in order to integrate its use into their daily routine in the long term. ‘Changing processes that have been learnt and implemented for years and decades is - logically - a big change for many employees,’ says Pries, adding: ’That's why we provided them with targeted training right from the start - and with great success.’
Exchange that promotes innovation
The close dialogue with Steffen Brand, Customer Success Manager at Logistikbude, was essential for the internal changeover. The fast, effective communication with immediate feedback convinced the PaLog team all round. Pries explains: ‘The collaboration is great fun. We still regularly exchange information and talk about new ideas that we can try out.’ According to Brand, the project also thrived on the feedback from employees:
‘The collaboration with PaLog and in particular with Carola Pries is also very valuable for us. Thanks to her many years of experience in load carrier management, we have not only gained important insights, but also created tangible added value together - for our employees as well as for the sustainable growth of the company.’
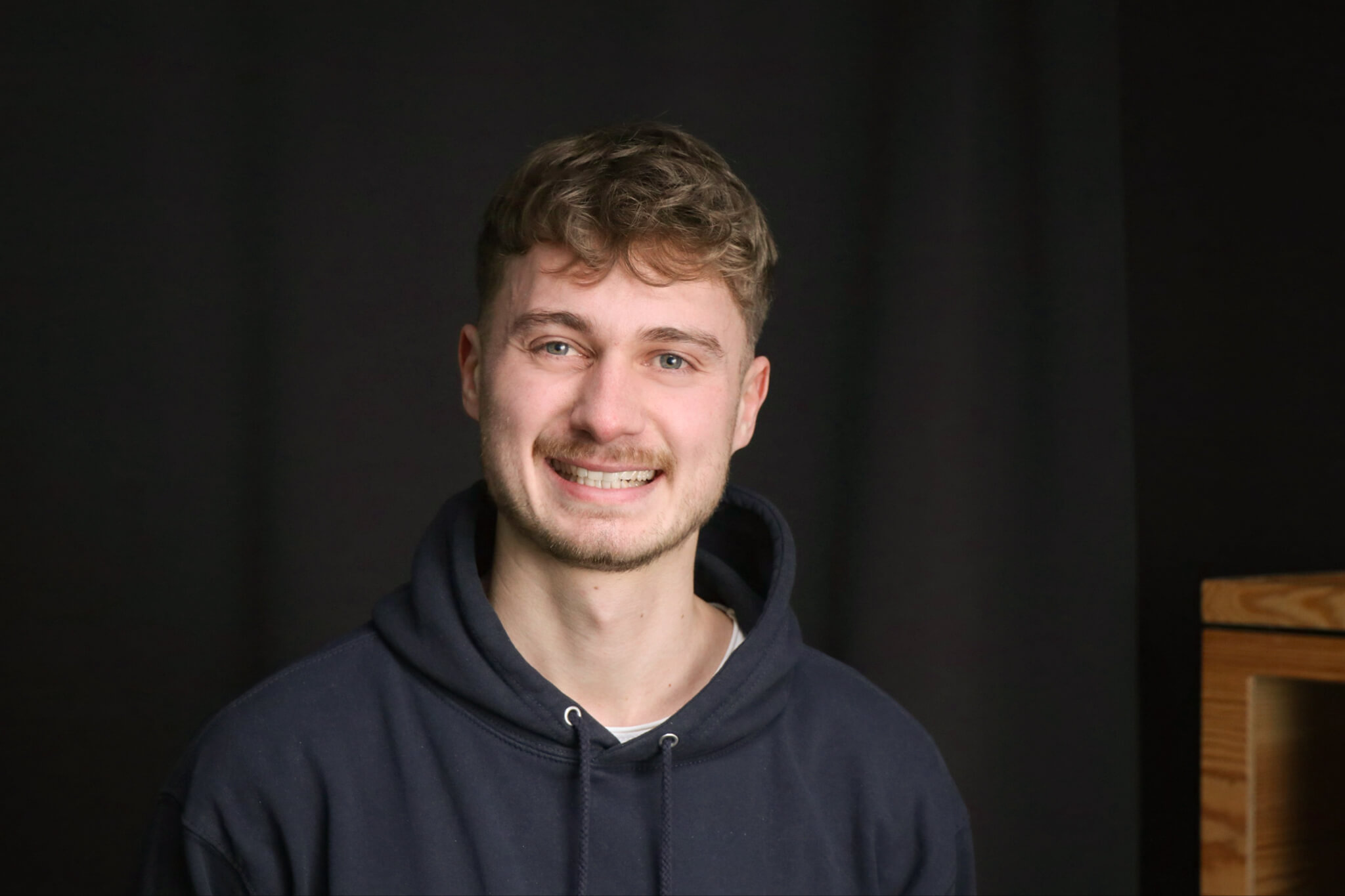
Serialisation of pallets opens up new perspectives
Even after the successful implementation, the PaLog team is working together with Logistikbude to further develop the solution and streamline more processes. While the digitally recorded bookings are currently still checked at the head office, this step could be fully automated in the future. The PALETTEN-SERVICE Hamburg Group is also currently testing the use of Euro pallets that are serialised using QR codes in order to further improve traceability.
‘In the long term, we want to develop this system further in order to track our load carriers even more efficiently. QR code technology opens up many new possibilities for us, with which we have already been able to inspire some of our customers,’ says Stadach.
About the Logistikbude:
Logistikbude was founded in 2021 and digitalises the management of reusable assets such as pallets, containers or racks used to transport goods. Its user-friendly software enables the transparent tracking of containers in real time and provides an overview of stocks, requirements and turnaround times. As a result, shippers, logistics service providers and retailers benefit from lower replenishment rates and reduced administrative costs - simply, efficiently and, above all, in a resource-saving manner. The experts at Logistikbude have incorporated their many years of experience in the packaging industry at Fraunhofer IML into the solution.
Schedule a free consultation now!
We would like to get to know you and your current challenges with reusable objects. As a first step, we analyse your status quo together and check where there is potential for optimization and automation. If we have a suitable solution for you, we will present our solution to you on your use case in a second appointment.