Container management at the limit: these 3 challenges cost you time, money and nerves - here's how you can finally get them under control
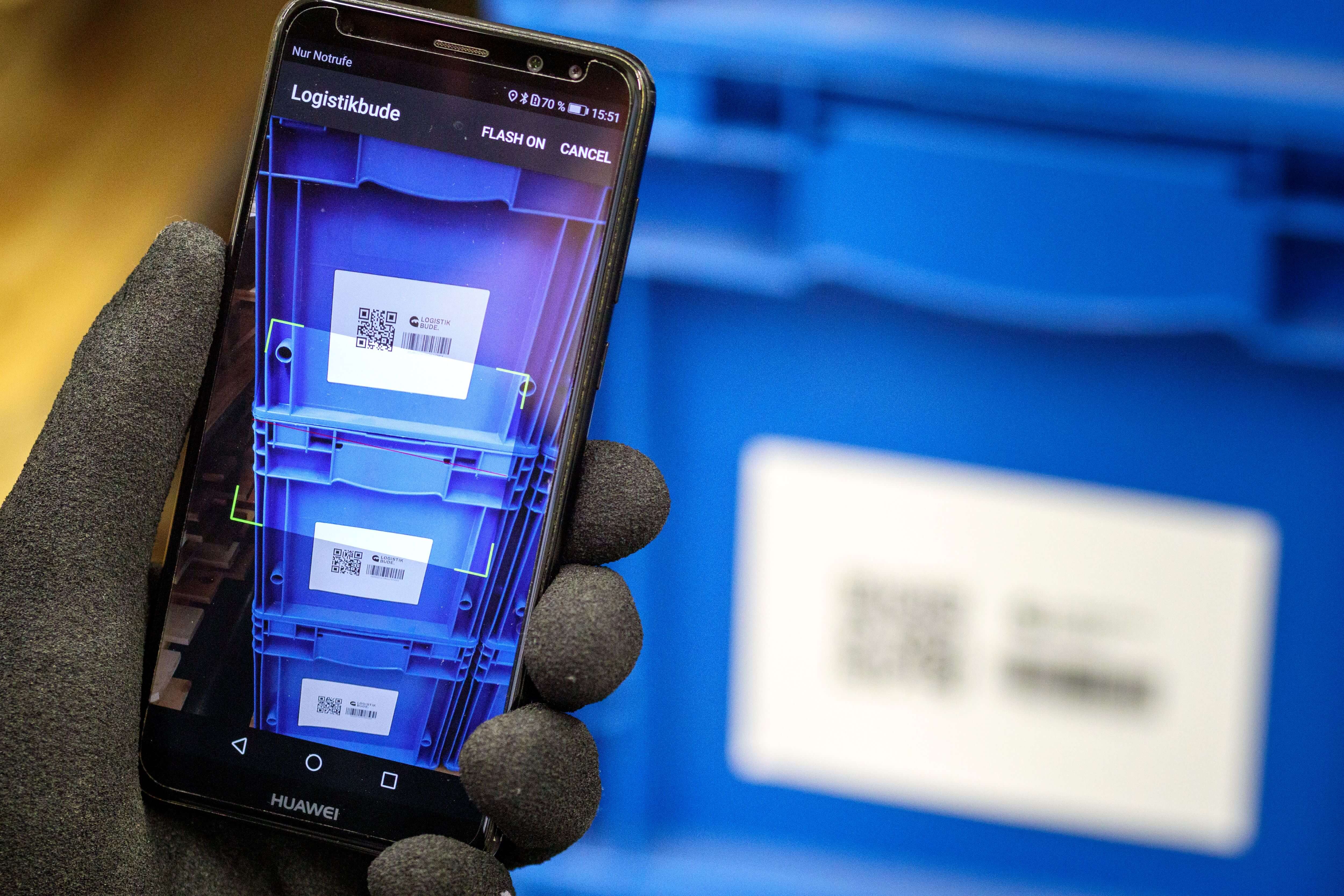
Anyone who has pallets, mesh boxes, containers or other reusable packaging in circulation knows the game: What is not actively tracked disappears. And faster than you can say ‘loading equipment account’.
In many companies, container management - and by that we mean all the returnable load carriers out there - not only causes high direct costs due to shrinkage and unnecessary reorders, but also a lot of hidden effort. Employees document bookings by hand, maintain Excel lists and make phone calls to the load carrier departments. That doesn't just sound old-fashioned - it is. And above all, it's expensive.
Effective container management is essential to avoid losses, inefficient utilisation and a lack of transparency in the supply chain. This is because poorly managed KLTs, pallets, mesh boxes, racks, etc. lead to:
- Increased costs due to unnecessary replacement purchases
- Delays in the logistics processes
- High personnel costs
- Frustration
Nevertheless, many companies continue to rely on manual processes or fragmented Excel solutions - with serious consequences.in this article you will learn how you can...
- prevents up to 25 % shrinkage of pallets and containers,
- save thousands of euros annually on replacement purchases,
- significantly reduces your labour costs
- and finally get an overview of where your load carriers really are.
In short: we show you the three biggest problems in container management - and how you can solve them easily, efficiently and permanently with a digital system.
The 3 biggest challenges in container management
1. lack of transparency & high shrinkage rates - when pallets are simply gone
According to a study by the German Logistics Association (BVL) and GS1 Germany, around 25% of load carriers are lost or remain untraceable in medium-sized companies every year. This means that pallets disappear by the dozen somewhere between the supplier, warehouse, haulage company and customer - and nobody knows exactly who can be charged for this loss.
The reasons are well known, but difficult to control: lack of traceability, no centralised systems, no consistent bookings. Movements are often not recorded at all or far too late - handwritten, on paper forms or in scattered Excel files stored somewhere on individual computers.
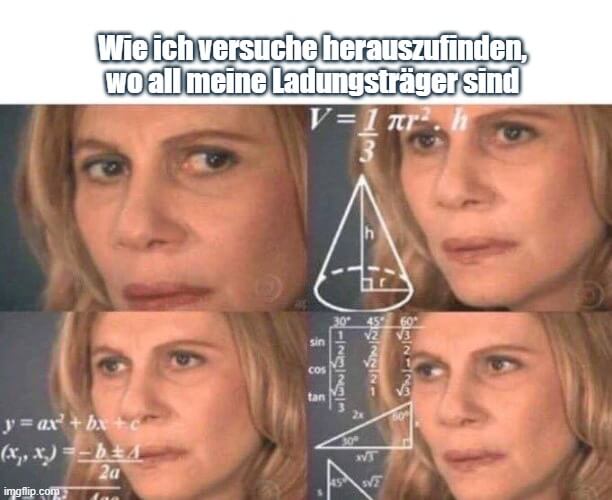
Practical example:
A medium-sized food producer loses around 15,000 pallets a year - that's 60 pallets per working day. At a unit price of €10, the direct loss adds up to over €150,000 per year. And that's just the tip of the iceberg: orders are delayed because pallets are missing. Customers are annoyed. And internally, valuable time is spent searching instead of doing taxes.
In short: the shrinkage not only eats up money - but also nerves.
2. high personnel costs - entire teams just for tracking pallets? Really now?
In many companies, entire ‘shadow teams’ deal exclusively with container management: manual bookings, Excel comparisons, email ping-pong, complaints with customers or freight forwarders - day after day.
According to a study by GS1 Germany and the German Logistics Association (BVL), almost 90% of companies still work with analogue or partially analogue processes - usually spread across several departments. In many cases, this means that one or more full-time positions are dedicated solely to tracking load carriers. Not to improve processes - but to avoid losing the overview completely.
Practical example:
In times of a shortage of skilled labour, people are desperately needed - not for strategic supply chain management, but for manually booking movements, reconciling accounts or creating shipping documents. Processes that could have been automated long ago.
Instead of relief for the team, there is paperwork 2.0.
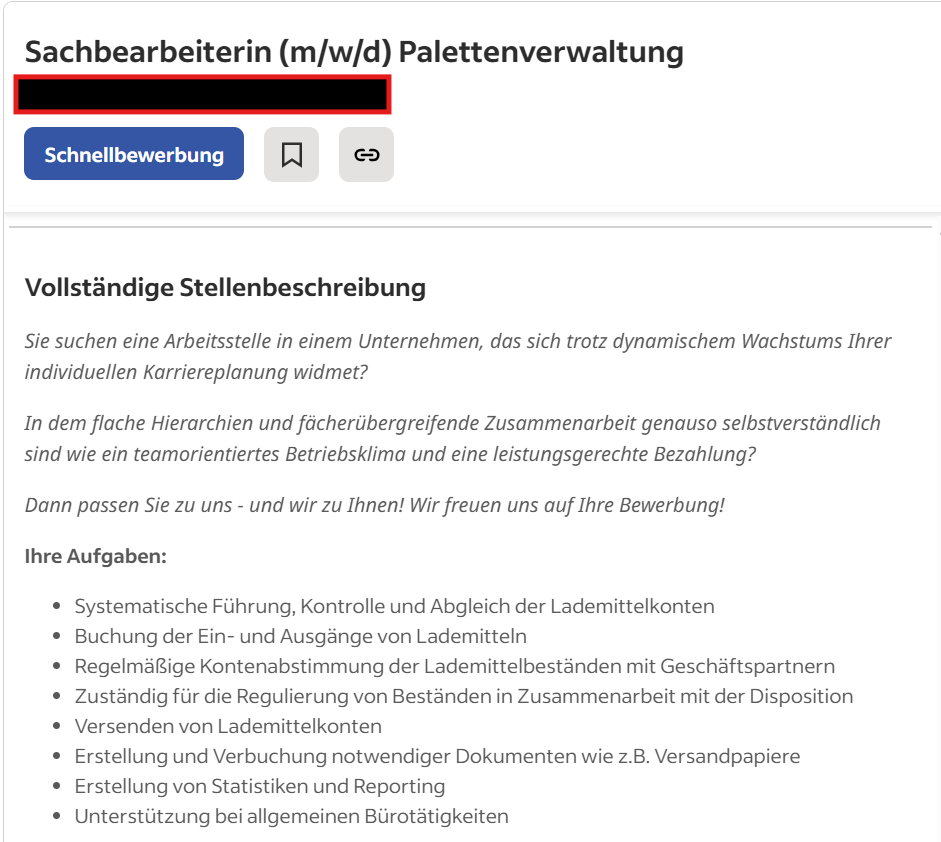
3. inefficient processes & uncontrolled costs - when Excel rules
Anyone who works with Excel lists knows the chaos: one file for goods receipt, one for goods issue, one for the customer, one for the supplier. Who posted what last? Unclear. What is still in circulation? Difficult. And woe betide anyone who opens the wrong version.
Practical example:
Experience shows that companies and their employees spend between 3-5 hours per week searching for missing load carriers - whether in the warehouse, in Excel lists or on the phone with partners. In a smaller company with five warehouse or dispatch employees, this adds up to over 100 hours per year - in other words, more than two complete working weeks just for searching.
In larger companies with several locations or hundreds of load carrier movements every day, we are quickly talking about weeks of time lost every year.
And that's just the beginning: incorrect bookings, duplicate orders, late deliveries - often the result of a lack of transparency. Reliable figures are lacking and decisions are based purely on gut feeling.
Excel may be versatile - but it's not a real load carrier system.
So you can finally bring order to the load carrier chaos:
Digital administration saves time, costs and nerves
Many of the problems mentioned can be solved quickly and sustainably with digital load carrier management. Instead of keeping track of bookings manually or comparing Excel lists, a centralised system takes over the entire administration: automated recording, seamless tracking and real-time inventory overview - all in one platform, also via an API interface.
What that means for you:
- You can see where your load carriers and containers are at all times.
- Losses and incorrect bookings are immediately visible - and avoidable.
- Searches, reconciliations and follow-up phone calls are completely eliminated.
- Employees are relieved and gain time for value-adding tasks.
The result: less shrinkage, less effort, lower costs - but significantly more transparency and control.
About the Logistikbude:
Logistikbude was founded in 2021 and digitalises the management of reusable assets such as pallets, containers or racks used to transport goods. Its user-friendly software enables the transparent tracking of containers in real time and provides an overview of stocks, requirements and turnaround times. As a result, shippers, logistics service providers and retailers benefit from lower replenishment rates and reduced administrative costs - simply, efficiently and, above all, in a resource-saving manner. The experts at Logistikbude have incorporated their many years of experience in the packaging industry at Fraunhofer IML into the solution.
Schedule a free consultation now!
We would like to get to know you and your current challenges with reusable objects. As a first step, we analyse your status quo together and check where there is potential for optimization and automation. If we have a suitable solution for you, we will present our solution to you on your use case in a second appointment.