Logistikbude optimises Nagel-Group's reusable management at all 130 company locations
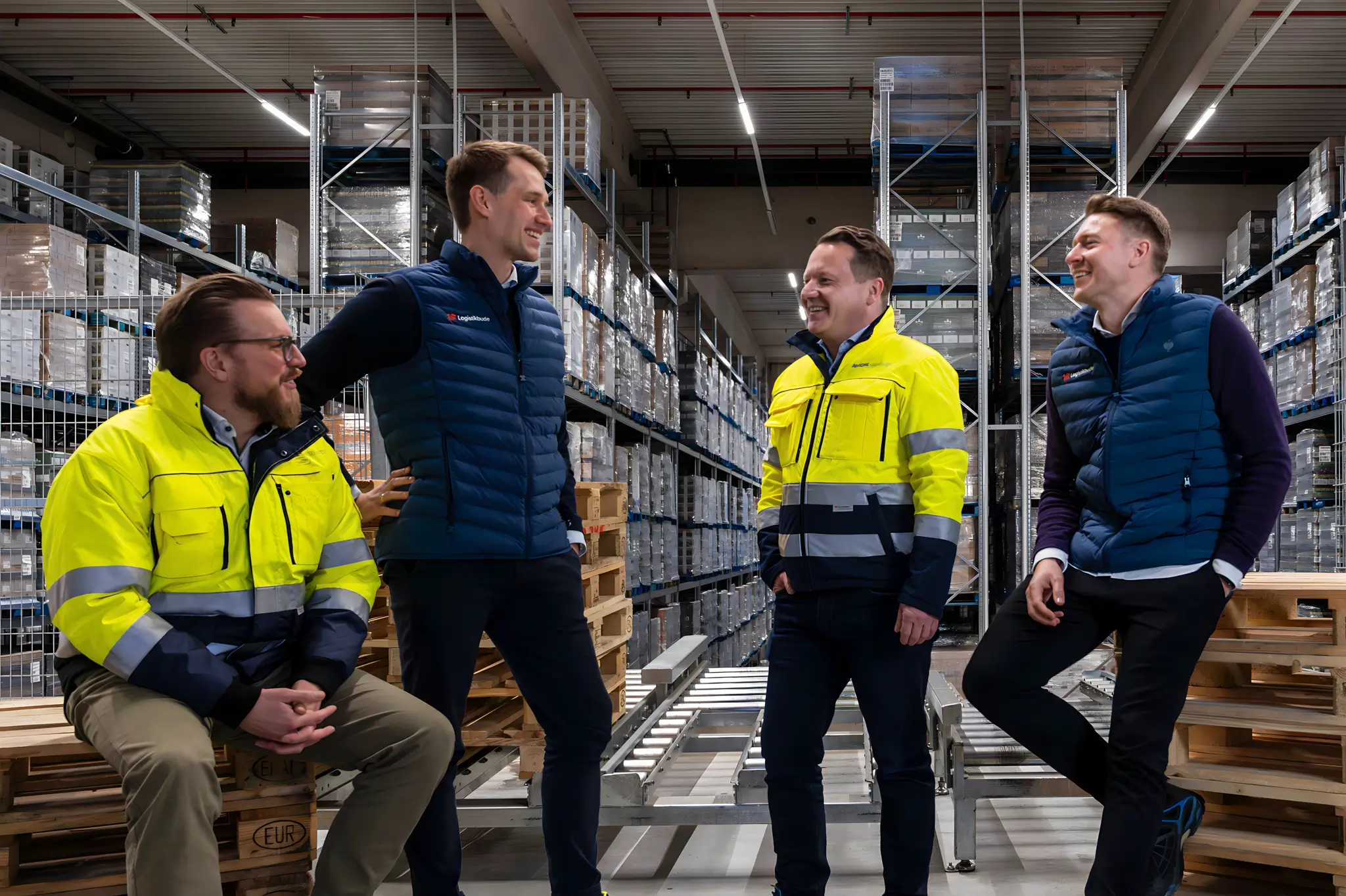
PRESS RELEASE
Company / Order
Logistikbude optimises Nagel-Group's reusable management at all company locations
- Cross-location implementation in the first half of the year
- Software enables digital management of all load carriers
- Efficient processes relieve employees
Dortmund / Hamburg, 05 February 2025 - Nagel-Group is relying on Logistikbude GmbH to optimise its reusable management: with its software solution of the same name, the Dortmund-based start-up enables the digital real-time management of reusable items such as pallets or Euroboxes at all 130 company locations. The Group is thus taking a further step in its digitalisation and sustainability strategy and is also simplifying internal administrative processes. As one of the leading food logistics companies in Europe, Nagel-Group transports goods in all consignment sizes and temperature classes. Full implementation of the solution should be completed in the first half of the year.
‘Transforming load carrier management for an industry player like Nagel-Group is an exciting project for us - and it also shows that there is a great need, especially in the transport and logistics industry, to digitise returnable management. Not only to save costs, but above all to relieve the burden on our own employees,’ says Dr Philipp Hüning, CEO and co-founder of Logistikbude.
The software solution developed at Fraunhofer IML makes all load carriers at Nagel-Group - from Euro pallets and plastic pallets (H1) to Euro boxes - digitally visible across all locations in real time. ‘In future, every load carrier that passes through the Nagel-Welt will be booked and reconciled by the logistics centre,’ says Hüning. This optimises coordination processes so that employees are relieved and can concentrate fully on their main activities. The digital visibility of the loading aids also reduces the repurchase rate, as Euroboxes cannot simply ‘disappear’ from the value chain. This saves emissions on the one hand and costs for avoidable new purchases on the other.
Reusable management of the future: transparency and automation
‘As one of the pioneers of digital transformation in the logistics industry, part of our strategy is to constantly optimise our processes in order to make our team's work as easy as possible and to use our resources efficiently,’ says Jens Kleiner, COO of Nagel-Group, about the collaboration with Nagel-Group. ‘Logistikbude's cloud-based software can be integrated directly into our existing processes and is therefore quickly ready for use - that convinced us straight away.’
The software solution also offers numerous helpful tools, including intelligent forecasting and inventory and requirements planning, which make it easier to manage your own load carrier stock. With the help of automated booking, recurring entries can be easily automated. Nagel-Group's customers also benefit from digitalised returnable management: they can also use a web link to track where the booked load carriers are, which significantly improves both communication with each other and customer satisfaction.
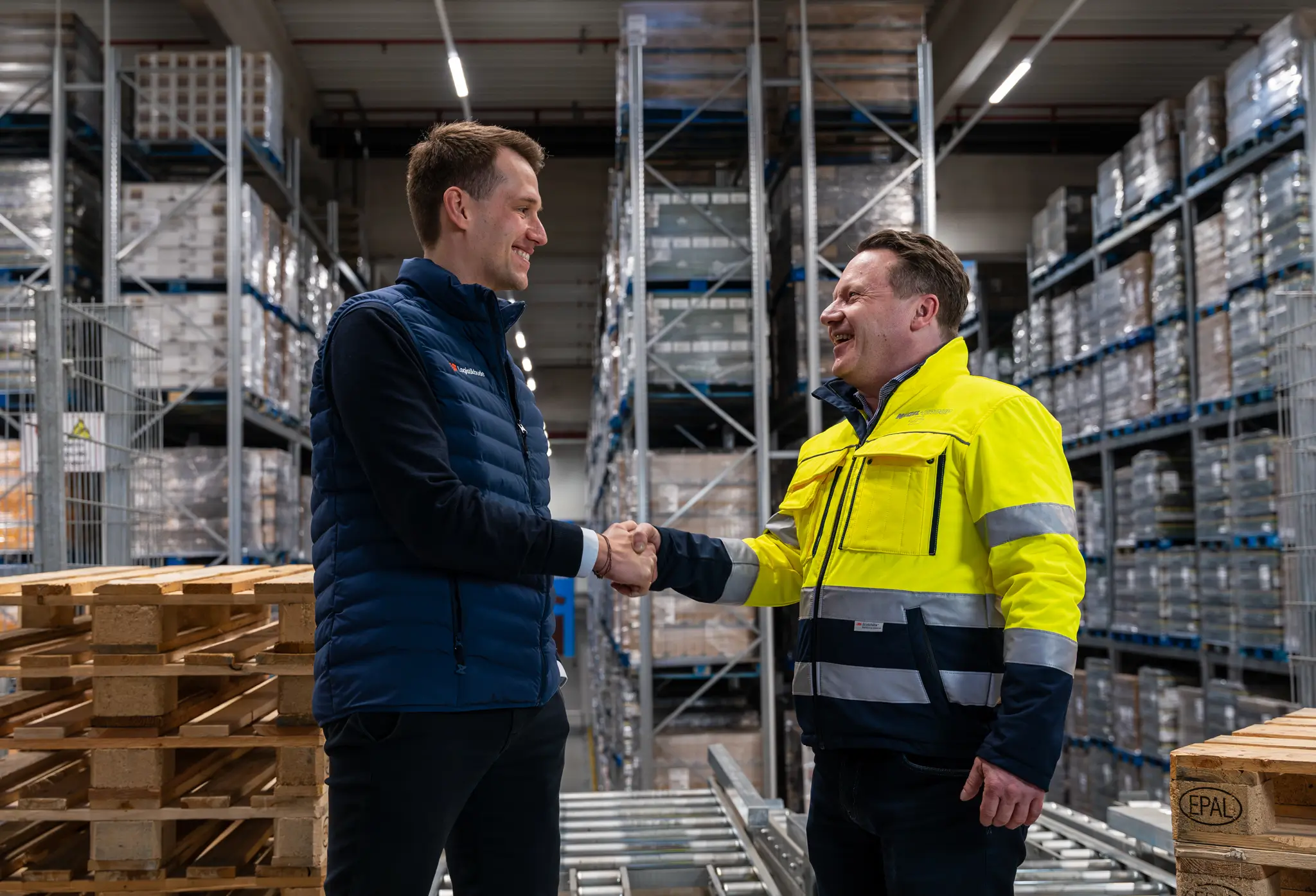
Implementing and continuously developing customised solutions
As the basis for the collaboration, the Logistikbude team took deep dives into the processes at various Nagel-Group sites and evaluated them. ‘In this way, we ensure that the functions of our software solution are optimally adapted to local requirements. We also implement employees' wishes and suggestions. They know their own processes best and will ultimately use our software solution,’ says Hüning. The company-wide implementation is expected to be completed in the first half of the year. At the same time, the software is constantly being further developed in order to respond to customer requirements, utilise technical developments and evolve with the market.
‘Our software is based on the latest technologies, such as artificial intelligence in image processing or the Internet of Things (IoT), which will only get better and more widespread in the coming years. We will also continuously refine and optimise our software solution for our partners.’
About the Nagel-Group
Nagel-Group stands for perfectly networked food logistics throughout Europe. At more than 130 locations, over 11,000 employees work every day to reliably supply Europe with food. Every day, the Group moves 105,000 consignments of a wide variety of foodstuffs in all consignment sizes and temperature classes. Most recently, the company generated a turnover of 2.2 billion euros. Find out more about Nagel-Group and how the company manages to deliver the right goods at the right time and in the right quality every day.
Further information about the Nagel-Group can be found at: www.nagel-group.com
Photographer: Sina Ramin Sadegh Nadi
Schedule a free consultation now!
We would like to get to know you and your current challenges with reusable objects. As a first step, we analyse your status quo together and check where there is potential for optimization and automation. If we have a suitable solution for you, we will present our solution to you on your use case in a second appointment.